Nanocomposite Inks for 3D Printing RF Devices

Lincoln Laboratory's custom-designed active mixing nozzle, integrated with a 3-axis motion-controlled 3D printer, uses specially tailored nanocomposite inks to additively manufacture radio-frequency (RF) devices with graded dielectric properties. The ability to control the electromagnetic properties of RF devices via material composition can facilitate the fabrication of components that have reduced size, weight, and power consumption yet accommodate large frequency bandwidths.
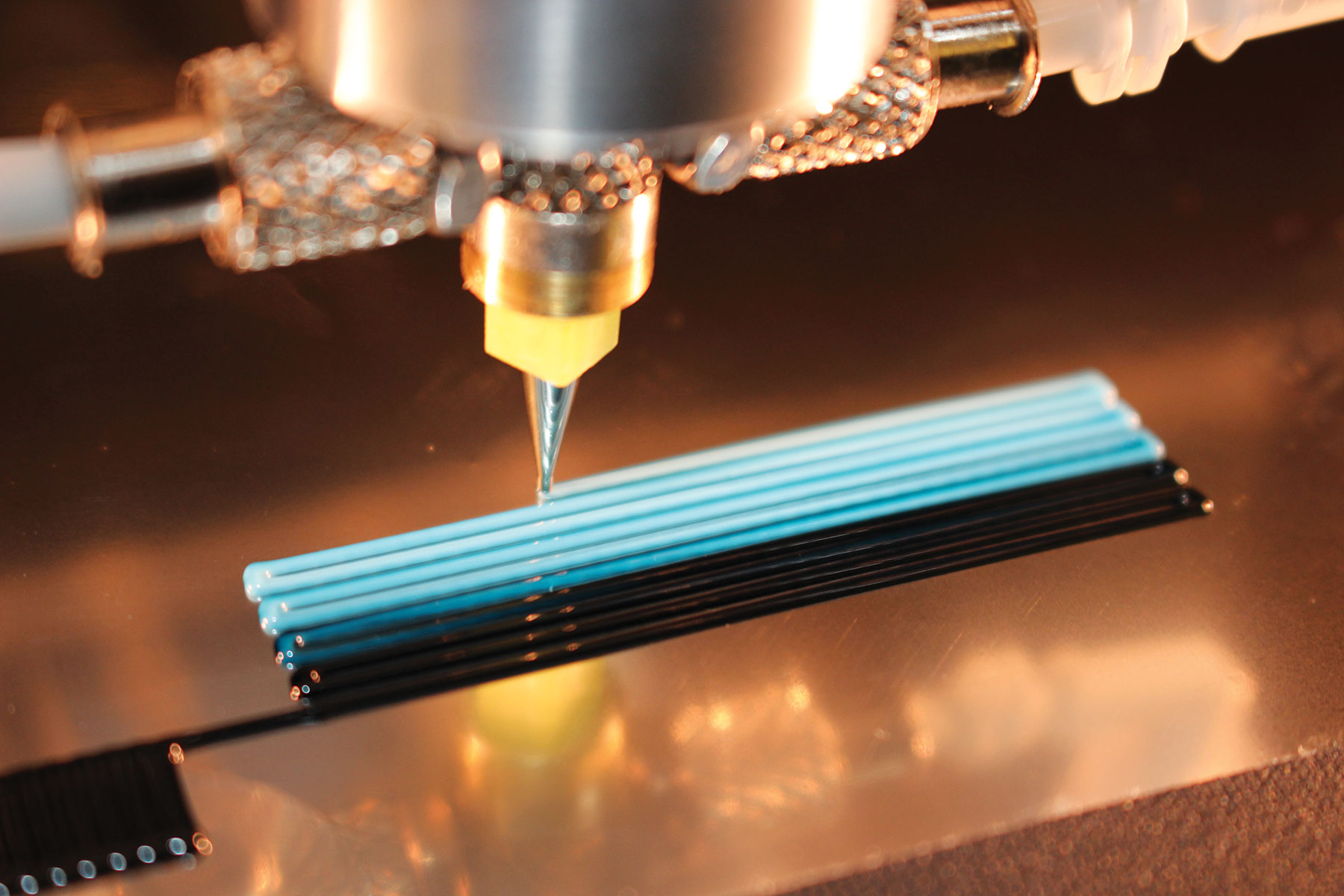
Challenge
Additive manufacturing, commonly called 3D printing, has enabled the rapid, economical production of a variety of RF devices (e.g., capacitors, antennas, inductors) that have been difficult, time-consuming, or costly to make because of their complicated designs. The increasing demand for miniaturized RF systems that accommodate large frequency bandwidths requires 3D printing devices with graded dielectric properties.
One current method to produce 3D-printed components with graded dielectric properties is to build the component of two spatially separated dielectric materials. The distinct interfaces between these disparate materials can lead to varying thermal expansion of the materials. Another technique is to place air voids within the component to control permittivity (i.e., electrical energy allocation). Both techniques typically yield mechanically unstable structures that limit device performance, especially for RF systems on small satellites and aircraft that operate in difficult environmental conditions.
Our Solution
The Laboratory has successfully developed new additive manufacturing materials that inherently achieve graded dielectric properties. Our nanocomposite inks, composed of block copolymers and oxide nanoparticles, are designed for direct ink writing. Once a critical pressure is reached, the inks flow through the nozzle and rapidly solidify to create the printed shape.
Through the active mixing of our novel nanocomposite inks, we have demonstrated the rapid design and fabrication of high-performance, temperature-stable RF devices. Measurements verified that the prototype waveguide resonator filters and lenses we manufactured achieved RF performance with low loss. We tailored the properties and dielectric behavior of the devices by altering the 3D printing inks' particle-to-polymer ratio via an active mixing printhead.
Benefits
- Produces mechanically robust parts suitable for use on platforms like drones or small satellites that face challenging environmental conditions
- Offers a wide range of printed composites whose relative permittivity can be engineered by varying the polymer-to-nanoparticle ratio during the additive manufacturing process
- Allows continuously graded dielectric performance, avoiding mismatches in the thermal expansion of the composite materials
- Uses a direct ink writing method to enable compositional and geometric control of the fabricated devices
Additional Resources
U.S. Patent 10,851,251; patent pending, US20190300741A1
More Information
B. Duncan et al., "Low-Loss Graded Dielectrics via Active Mixing of Nanocomposite Inks during 3D Printing," Advanced Materials Technology, 11 November 2022.
2024 R&D 100 Award winner